Cleaning more thoroughly and frequently with fewer staff members continues to be a challenge for many facilities. COVID-19 forever changed the way the world approaches cleaning, but it also shined a spotlight on the cleaning industry and how people can maintain clean and healthy environments with the help of reliable and effective technology.
From production facilities and restaurants to airports and hotels, every type and size of facility has had to take a close look at its cleaning and disinfecting protocols to adapt to the new normal. With the stakes at an all-time high, it’s essential that facility managers focus on using the right chemical concentrations that can help remove dangerous pathogens and restore public confidence.
Keep a close watch on cleaning concentrations
While it’s critical that facilities adapt to new and improved cleaning and disinfection protocols, it’s just as important to ensure employees understand that the amount of chemical they use has an impact on cleaning results. Many cleaning programs use chemical concentrates to reduce reliance on ready-to-use products that are more costly and less environmentally friendly to transport. Staff must dilute these cleaning solutions before use.
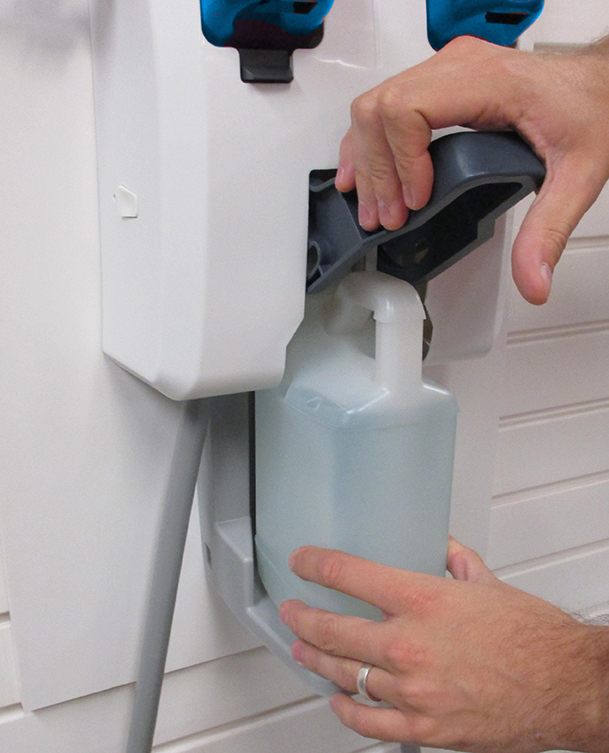
Chemical dispensing systems are designed to deliver the right concentrations for different products. Image courtesy of Hydro Systems
To remove dangerous pathogens and create a clean, healthy space, it’s vital that facility managers have solutions in place to uphold proper chemical dilutions. Thankfully, chemical dispensing systems are designed to deliver the right concentrations for different products. This delivers multiple benefits, including:
1. Improved product performance—Chemical dispensers properly dilute chemicals, ensuring there isn’t too little or too much chemical, to effectively clean surfaces the first time. If too much chemical is used, it can leave behind sticky residues or damage surfaces. If the opposite occurs, surfaces will not be properly cleaned or disinfected, potentially leaving behind harmful germs and negatively impacting a customer’s experience or brand reputation.
2. Reduced resource waste—Improperly measured chemical results in poor performance and increases rewash rates, leading to wasted chemical, water, and energy. Due to the high demand of disposable and single-use products throughout the COVID-19 pandemic, experts predict that consumer demand for sustainable practices will be at an all-time high in the near future. Businesses must consider methods they can implement to cut back on unnecessary waste.
3. Enhanced employee safety—When chemicals are used at the wrong concentrations, it can put employees at risk of inhaling toxic fumes or experiencing skin or eye irritation. Whether a cleaning team uses just two cleaning chemicals or closer to 10, facility managers must reduce employee exposure to potentially hazardous chemicals. By guaranteeing the use of chemicals in the right concentrations, dispensers eliminate the need to measure chemicals by hand, reducing the chances of harmful reactions and chemical burns as well as potential slip and fall accidents that can result in time away from work.
4. Time and labor savings—Cleaning surfaces right the first time leads to enhanced productivity, allowing staff to move on to additional important tasks. Labor is often the highest cost for any cleaning program, so finding ways to make employees more productive and reduce repetitive efforts can contribute to noticeable savings over time.
The download on chemical dispensers
There are numerous types of dispensers on the market. Use the following tips to select the best dispenser for your operation:
- Seek out proper dilution control. Dilution variance can impact the effectiveness of a cleaning solution and result in improper results.
- Consider portable spraying and foaming capabilities. Spraying large areas or using foaming features speeds up the cleaning process while also ensuring chemicals remain on surfaces for the recommended dwell time. This is especially helpful in restrooms and kitchens that have a lot of hard-to-reach areas.
- Watch out for backflow. Different dispensers feature different types of eductors. Some may provide backflow protection through the use of an elastometric sleeve, while others utilize a small gap of air between the water source and chemical inlet.
- Make room for multiple products. If you’re using multiple cleaning chemicals, or anticipate having to add more in the future, look for dispensers that can house numerous products.
- Find a user-friendly interface. Install chemical dispensers that offer simple, straight-forward directions to encourage employees at all levels to use the system frequently and confidently.
Time to shine
Prior to COVID-19, the cleaning industry wasn’t always seen as essential. Hotel housekeepers completed their work out of sight of guests. School and office custodians typically showed up to clean after hours so building occupants were greeted with a welcoming environment the next day. Today, the curtain has lifted, revealing the important work facility managers, building service contractors and other cleaning teams do every day to improve the health and safety of building residents, customers and visitors. With the help of tools like chemical dispensing systems and other innovative solutions, facilities and their staff will continue to shine before, during and well after this unprecedented time.